Ventajas de la prueba de motores de CC mediante el análisis del circuito del motor
Las pruebas eléctricas de motores eléctricos de corriente continua (CC) son un reto tanto para la industria como para los centros de fabricación y reparación. La cuestión clave tiene que ver con la capacidad de comparar una bobina con la siguiente, en caso de que no se facilite información exacta. En este artículo se tratará la cuestión de las pruebas sencillas para aumentar la confianza de las conclusiones de las pruebas y los análisis mediante el Análisis de Circuitos de Motores (ACM).
El término MCA procede de un método de ensayo que proporciona información sobre los componentes básicos de un motor eléctrico de CA o CC. Estos componentes básicos incluyen:
- Resistencia, medida en Ohmios
- Impedancia, medida en Ohmios
- Inductancia, medida en Henries
- El ángulo de fase del devanado de inducción, medido en grados
- Resistencia de aislamiento, medida en Meg-Ohms
El instrumento al que nos referiremos en este artículo proporciona estas lecturas generando una señal de corriente alterna (impedancia, inductancia, ángulo de fase) de baja tensión y onda sinusoidal real a frecuencias de 100 a 800 hercios, una señal de corriente continua de baja tensión para la resistencia y 500 ó 1.000 voltios de corriente continua para la prueba de resistencia del aislamiento.
Además, se realiza una prueba especial denominada I/F en la que se duplica la frecuencia aplicada y se obtiene una relación a partir del cambio en la impedancia del bobinado. Esta prueba se introduce para identificar los primeros cortocircuitos que puedan existir en el devanado. Utilizando los datos aplicados, se puede evaluar el estado del bobinado de un motor de CC mediante comparaciones de bobinas, comparaciones con lecturas conocidas o mediante tendencias de cambios en los bobinados a lo largo de un periodo de tiempo.
Los motores eléctricos de CC que se incluirán en este artículo son motores de CC en serie, en derivación y compuestos. Algunas de las pruebas básicas descritas pueden realizarse en imanes permanentes, servos de CC, máquinas herramienta de CC y otros (aunque los motores de CC sin escobillas se evalúan de forma similar a los motores de CA). Los tipos de motores eléctricos de CC pueden describirse por sus bobinados y conexiones.
Teoría de los motores de CC
Los motores eléctricos de corriente continua funcionan según un principio básico de la electricidad: la interacción entre dos campos magnéticos situados en un ángulo entre sí se atraen/repelen dando lugar al movimiento. En el caso de un motor eléctrico de corriente continua, la potencia se suministra a un campo estator y a un inducido que crean campos magnéticos que están, eléctricamente, a unos 90 grados el uno del otro. La atracción/repulsión resultante del inducido respecto al campo genera un par y el inducido gira.
Los componentes básicos de un motor eléctrico de CC incluyen:
- Bastidor – Constituye la estructura exterior de la máquina. Se utiliza para montar la mayoría de los demás componentes del motor
- Campos – Son bobinas montadas sobre piezas polares de campo que generan un campo magnético estacionario.
- Interpolos – Son bobinas que se colocan entre las bobinas de campo y que generan un campo que se utiliza para evitar el chispeo excesivo de las escobillas.
- Testeros – También llamados alojamientos de cojinetes, se utilizan para alojar las escobillas y el aparejo de escobillas, y para alojar los cojinetes del eje, manteniendo el inducido centrado en el bastidor.
- Aparejo de esco billas – Sujeta y posiciona las escobillas por encima del conmutador del inducido. Normalmente, se utiliza un dispositivo de tensión para mantener una presión constante sobre los cepillos.
- Escobillas – Se utilizan para proporcionar corriente continua al inducido. Las escobillas van sobre el colector.
- Conmutador – Consiste en muchas barras de cobre separadas por mica. Cada barra está conectada a las bobinas del inducido.
- Armadura – Es la parte giratoria del motor que contiene bobinas.
A diferencia de la mayoría de los motores de corriente alterna, los motores de corriente continua requieren alimentación separada para los campos y el inducido. La CC suministrada a los campos del estator genera un conjunto de campos Norte y Sur constantes. La CC suministrada al inducido genera campos Norte y Sur que están a 90 grados eléctricos del campo estacionario.
A medida que el inducido genera par y se desplaza hacia el polo Norte o Sur correspondiente, las escobillas cambian de posición en el conmutador, energizando otro conjunto de bobinas a 90 grados eléctricos del campo estacionario. En realidad, esto convierte al inducido en un componente de corriente alterna, ya que la corriente se desplazará en una dirección, en función de la posición de las escobillas, y luego en otra dirección a medida que el motor funcione.
Las escobillas se colocan en una posición eléctricamente “neutra” (sin corriente inducida por los campos del estator) para reducir las chispas. En la mayoría de las conexiones de motores de corriente continua, la velocidad de funcionamiento puede modificarse variando la tensión del inducido. Un peligro general inherente a los motores de CC es que si se pierde la corriente de campo mientras se mantiene la corriente del inducido, el motor puede despegar y la velocidad aumenta hasta que el inducido se autodestruye.
Los tres tipos básicos de bobinado que pueden utilizarse para identificar el tipo de motor de CC son:
- Serie: Normalmente se encuentran en aplicaciones que necesitan un alto par de arranque. Constan de un conjunto de bobinados de campo de hilo grande y relativamente pocas vueltas, marcados como S1 y S2, que se conectan en serie a los interpolos y al inducido, marcados como A1 y A2 (véase la figura 1). Los motores conectados en serie se utilizan normalmente como motores de tracción y tienen una resistencia básica muy baja.
- Derivación: Normalmente se encuentra en aplicaciones que requieren velocidad constante. Constan de un conjunto de bobinados de campo de alambre más pequeño con muchas vueltas, marcados F1 y F2 para la tensión simple y F1, F2, F3 y F4 para la tensión doble, y A1 y A2 para los interpolos y el inducido (Ver Figuras 2). Los motores conectados en derivación se utilizan normalmente como motores de grúas y máquinas herramienta y tienen una resistencia básica relativamente alta.
- Compuesto: Combina las ventajas de los motores bobinados en serie y en derivación. Proporcionan un par relativamente alto con una resistencia básica a un cambio en la velocidad de funcionamiento. Las conexiones combinan las conexiones en serie y en derivación (véase la figura 3). Los motores compuestos son los más comunes y suelen encontrarse en la fabricación industrial.
Como se puede ver, hay pocas bobinas para comparar entre sí en una máquina de CC ensamblada. Sin embargo, se pueden desarrollar procedimientos para las pruebas de bobinado que proporcionen un alto nivel de confianza en los resultados de las pruebas.
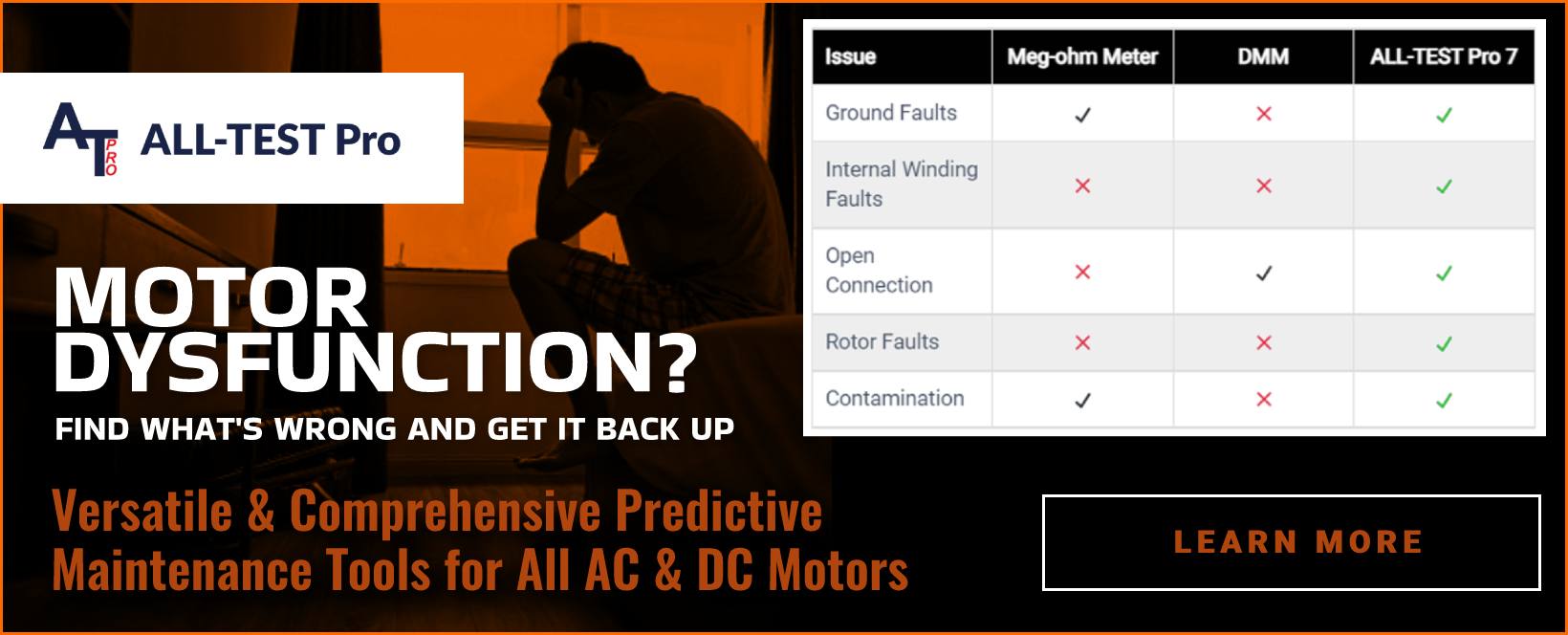
Fallos eléctricos comunes de los motores de CC
Existen una serie de fallos eléctricos comunes en los motores de corriente continua, de los cuales describiremos aquí los más frecuentes. Son el resultado de problemas específicos del diseño de los motores de CC como consecuencia de la temperatura, la fricción y los contaminantes internos como el carbono o el grafito.
Una de las causas más comunes de fallos en el bobinado de un motor de corriente continua es la contaminación del bobinado por polvo de carbón o grafito (carbono) procedente de las escobillas. El polvo fino impregna todos los devanados estacionarios y giratorios y creará un camino entre conductores o entre conductores a tierra. A menudo, la carbonilla queda atrapada y los problemas se agravan aún más con las prácticas de limpieza y mantenimiento cuando se sopla con aire comprimido o se limpia y se hornea el inducido. En ambos casos, la carbonilla puede apelmazarse en las esquinas, normalmente justo detrás del conmutador. Esto terminará como un fallo a tierra o un cortocircuito de espiras justo en la conexión del conmutador.
Otro fallo común, que a menudo no se tiene en cuenta, es la refrigeración de la máquina de CC. Esto puede ocurrir porque los conductos de refrigeración están bloqueados, porque el inducido gira demasiado despacio sin refrigeración adicional o porque los filtros están sucios (el fallo más común relacionado con la refrigeración). La temperatura es el mayor enemigo de los equipos eléctricos, sobre todo del sistema de aislamiento, cuya vida útil se reducirá a la mitad por cada 10 grados centígrados de aumento de temperatura (regla empírica aceptada). A medida que el aislamiento se debilita, su fiabilidad disminuye hasta que se producen fallos de bobinado entre espiras. Además de degradarse el sistema de aislamiento, las escobillas también se degradan más rápidamente, lo que provoca un mayor desgaste del conmutador y una contaminación adicional por carbono de los devanados.
Otro fallo que está relacionado con el calor se genera a partir de prácticas que tienen los campos energizados con el inducido en reposo (desenergizado). Este es un modo común de funcionamiento que requiere un ventilador separado para proporcionar refrigeración al motor que normalmente tiene filtros que deben mantenerse limpios. Normalmente, este tipo de avería provoca un cortocircuito en las bobinas de derivación, lo que reduce la capacidad del motor para producir par, y puede terminar con la peligrosa condición de exceso de velocidad del inducido si no se mantiene adecuadamente.
El conmutador también ofrece posibilidades de averías, así como un indicador del funcionamiento y el estado del motor. Un motor de corriente continua que funcione correctamente tendrá una fina capa de carbón en el conmutador y las barras tendrán un aspecto uniforme. Las barras del colector quemadas, el cristal rayado, la carbonilla pesada o el colector sobrecalentado indican problemas potenciales que deben solucionarse.
Pruebas de armaduras
Las armaduras de CC son los componentes que requieren más tiempo, pero los más fáciles de comprobar. Se presentarán tres métodos básicos: trending, assembled y disassembled. Sin embargo, en el caso de las pruebas montadas y desmontadas se utilizará una medición de impedancia barra a barra. La impedancia se tiene en cuenta porque el inducido es un componente de CA y las simples mediciones de resistencia pueden pasar por alto algunos fallos, incluidos los cortocircuitos y las conexiones a tierra. La tendencia se revisará en un procedimiento general de tendencia para motores de CC más adelante en este artículo.
Cuando se comprueba el inducido de un motor de CC montado, el mejor método es realizar lo que comúnmente se conoce como prueba barra a barra utilizando las escobillas del motor. En el caso de un motor de corriente continua que tiene dos escobillas, no es necesario levantar ninguna de las escobillas, en el caso de un motor de corriente continua que tiene cuatro o más juegos de escobillas, es necesario levantar todas menos dos juegos a 90 grados entre sí, lo que las saca del circuito de prueba. Asegúrese de que se mantiene un buen contacto en el conmutador asegurándose de que más del 90% de la escobilla está en contacto con las barras del conmutador y de que las barras del conmutador están limpias. Si no están limpios, pula la armadura suavemente, utilizando un método aprobado, antes de la prueba. Si el colector está muy desgastado, será necesario desmontarlo y “girar y rebajar” el colector, en cuyo caso sería adecuado realizar una prueba barra a barra desmontada. Una vez ajustada, marque la posición de una barra en el colector y, a continuación, lleve la barra a una posición en la que quede justo debajo del borde de ataque de una de las escobillas. En la prueba montada, probablemente cubrirá al menos una barra y media con el cepillo. Realice una prueba de impedancia, anote la lectura y mueva el inducido de modo que el borde delantero de la escobilla esté sobre la siguiente barra conmutadora. Tome la siguiente lectura de impedancia y continúe hasta que cada barra haya sido probada. Un buen resultado mostrará un patrón consistente, mientras que un patrón inconsistente identificará una armadura pobre.
La prueba barra a barra desmontada es similar a la prueba montada, con la diferencia de que el inducido está fuera del bastidor y el comprobador tiene pleno acceso al conmutador. En este caso, el comprobador utilizará un accesorio de armadura o cables de prueba para conectar de barra a barra. La separación entre cada lectura de impedancia debe ser constante y de unos 90 a 180 grados entre sí. La primera barra debe marcarse y la prueba continúa hasta que una pata del dispositivo de prueba o del cable de prueba haya dado una vuelta de 360 grados alrededor del conmutador. Marque la impedancia para cada prueba de barra a barra y, a continuación, compruebe que existe un patrón coherente.
Pruebas de motores en serie
Los motores eléctricos en serie son muy difíciles de localizar, ya que no proporcionan conjuntos de campos con los que comparar. Las lecturas pueden tomarse de S1 a S2 y de A1 a A2 y, a continuación, trazar una tendencia a lo largo del tiempo o compararse con otras máquinas similares.
Al trazar las lecturas a lo largo del tiempo, las lecturas de resistencia simple deben corregirse en función de la temperatura, normalmente en relación con 25oC. La impedancia y la inductancia normalmente tienen un cambio limitado debido a la temperatura, mientras que el ángulo de fase y las lecturas de I/F permanecerán constantes, independientemente de la temperatura. Las variaciones en la I/F y el ángulo de fase indicarán espiras en cortocircuito, mientras que los cambios en la Impedancia y la Inductancia indicarán normalmente bobinados sucios.
La comparación de motores similares requerirá información adicional. El operador tendrá que asegurarse de que el motor es del mismo fabricante y diseño, así como de la velocidad, potencia, etc. El motor “modelo” debe ser nuevo o reconstruido según las especificaciones del fabricante original. Cuando se realizan lecturas comparativas, la temperatura de prueba debe ser similar de un motor a otro, sin embargo, las lecturas de I/F y ángulo de fase pueden compararse directamente. Estas lecturas no deben cambiar más de +/- 2 puntos para I/F y +/- 1 grado para ángulo de fase. Un error común cuando se reconstruyen devanados de campo en serie, aunque menos común que en las bobinas en derivación, es una sustitución incorrecta del tamaño del cable, lo que afectará a la capacidad del motor para generar par.
Pruebas de motores en derivación
Los motores shunt de doble tensión ofrecen la posibilidad de comparar dos conjuntos de bobinados, mientras que los motores de tensión única tendrán el mismo procedimiento de prueba que los bobinados de motores en serie, utilizando F1 a F2 en lugar de S1 a S2.
Con doble tensión, los devanados de derivación se etiquetan de F1 a F2 y de F3 a F4, lo que permite al analista probar y comparar estos dos conjuntos de devanados.
Al comprobar y solucionar problemas de las lecturas a lo largo del tiempo, las lecturas de resistencia simple deben corregirse en función de la temperatura, normalmente en relación con 25oC. La impedancia y la inductancia cambiarán más que en un motor bobinado en serie debido a la mayor resistencia simple del circuito. El ángulo de fase y la I/F permanecerán constantes, entre 1 y 2 puntos, independientemente de la temperatura. Las variaciones en la I/F y el ángulo de fase indicarán espiras en cortocircuito, mientras que los cambios en la Impedancia y la Inductancia indicarán normalmente bobinados sucios. Las comparaciones entre F1 y F2 y F3 y F4 deben ser inferiores al 3% en resistencia, inductancia e impedancia y no más de 1 punto de diferencia en I/F o ángulo de fase.
Los motores similares pueden probarse y compararse igual que los motores bobinados en serie. En la medida de lo posible, los motores deben probarse a la misma temperatura que las pruebas anteriores. Por ejemplo, unos minutos después de apagar el equipo en funcionamiento o antes de ponerlo en marcha, lo que permite realizar las pruebas a temperaturas similares.
Prueba del motor de CC compuesto
Las pruebas in situ, las tendencias y la resolución de problemas son mucho más sencillas con un motor compuesto. Los motores compuestos de tensión única se etiquetan normalmente de A1 a A2, de S1 a S2 y de F1 a F2, y los motores compuestos de tensión doble se etiquetan normalmente de A1 a A2, de S1 a S2, de F1 a F2 y de F3 a F4. Un punto adicional clave de un motor de devanado compuesto es que el devanado en serie normalmente se enrolla sobre el devanado en derivación, lo que permite posibles fallos entre estos dos devanados.
Si se trata de un motor compuesto, las pruebas se toman normalmente de los bornes del accionamiento de CC. Las pruebas MCA estándar que utilizan ALL-TEST implican señales de baja tensión y alta frecuencia que no dañarán la electrónica de salida del equipo, lo que reduce la necesidad de desconectar los cables del variador mientras se realizan las pruebas. Sin embargo, si el analista desea comprobar la resistencia del aislamiento entre los devanados en serie y en derivación, los cables deben desconectarse del accionamiento. Cuando la tendencia de la unidad de CC, prueba A1 a S2 y los dos cables de campo a continuación, realizar una prueba de resistencia de aislamiento de 500 voltios entre los cables S2 y F1 y comparar con las pruebas anteriores o motores similares, en cualquier caso, las lecturas de resistencia de aislamiento deben permanecer por encima de 100 Meg-Ohms.
La unidad ALL-TEST permite al analizador comparar inmediatamente las lecturas pasadas con las presentes a modo de comprobación rápida, lo que permite al analizador tomar una decisión rápida para seguir probando los devanados. Como se mencionó en las técnicas de prueba de motores en serie y en derivación, las lecturas de I/F y ángulo de fase no deben cambiar más de 1 punto entre pruebas, sin embargo, con el tiempo, los devanados en serie y de campo variarán drásticamente entre sí.
La localización de averías en motores compuestos debe realizarse en el propio motor. Desconecte todos los cables del motor y sepárelos. Pruebe los devanados en serie y de campo como se indica en las instrucciones de los devanados en serie y en derivación, luego realice una prueba de resistencia de aislamiento entre los devanados en serie y en derivación, la resistencia de aislamiento debe ser superior a 100 Meg-Ohms.
MCA DC Motor Testing Notes
Se pueden hacer varios puntos clave utilizando la prueba MCA en cualquier tipo de motor de CC:
- Cualquier lectura I/F fuera del rango de -15 a -50, por ejemplo, -56, indica un fallo del bobinado.
- Si la prueba muestra una resistencia infinita entre los cables del mismo circuito indica un bobinado abierto.
- Un aumento de la resistencia simple entre las pruebas, cuando se corrige en función de la temperatura, indica una conexión floja, en particular cuando cambian las lecturas de impedancia e inductancia. Una resistencia simple reducida, cuando se corrige en función de la temperatura, puede indicar un cortocircuito, normalmente acompañado de cambios en la impedancia, inductancia, ángulo de fase e I/F.
- Cuando se prueban motores similares, la I/F y el ángulo de fase no deberían cambiar más de 2 puntos, cualquier diferencia superior a esto debería provocar un análisis completo.
- Los cambios que se produzcan al realizar la prueba a través del circuito de inducido deben provocar una prueba barra a barra.
Siguiendo estas sencillas instrucciones, el uso de un dispositivo MCA le permitirá detectar los primeros fallos mucho antes de que el equipo falle durante su funcionamiento. Si se realizan pruebas como parte de un programa de mantenimiento predictivo, el intervalo debe ser como mínimo el indicado en la Tabla 1.
Tabla 1: Frecuencia de prueba del motor de CC
Tipo de prueba | No crítico | General | Crítica |
Mantenimiento general | 1 año | 6-9 meses | 3-6 meses |
Mantenimiento predictivo | 6 meses | 3 meses | 1 mes |
Prueba del inducido | 1 año | 6 meses | 3 meses |
Las pruebas de mantenimiento general son aquellas que no tienen tendencia en el tiempo. Suele ir acompañado de vibración, engrase de cojinetes, inspección del colector e inspección de escobillas. Las pruebas de mantenimiento predictivo normalmente implican lecturas de tendencias a lo largo del tiempo con el fin de detectar posibles fallos y, a continuación, determinar el mejor momento para retirar el motor para un mantenimiento correctivo. Una vez detectado un posible fallo, la frecuencia de las pruebas debe aumentar hasta que se determine que es necesario retirar el motor. Se debe realizar una prueba completa del inducido junto con una prueba de mantenimiento general o predictivo debido a las altas tensiones en el conmutador y la contaminación por carbón.
Conclusión
Las pruebas eléctricas generales de motores eléctricos de corriente continua son mucho más sencillas gracias a las nuevas técnicas disponibles con el análisis estático de circuitos de motores. Por primera vez, es posible detectar con antelación fallos en los devanados en serie, en derivación y en el inducido antes de que dejen fuera de servicio a los equipos. Las pruebas de mantenimiento predictivo pueden realizarse desde el accionamiento, mientras que las pruebas de localización de averías se realizan en el motor. En general, las pruebas son relativamente rápidas y requieren menos de cinco minutos por motor para las pruebas de mantenimiento predictivo, con el tiempo adicional necesario para la resolución de problemas. En general, las pruebas de MCA mejoran drásticamente las pruebas de motores de CC con respecto a los métodos tradicionales de pruebas de continuidad.
Sobre el autor
El Dr. Howard W. Penrose lleva más de 15 años en el sector de la reparación de motores eléctricos. Empezó como oficial de reparación de motores eléctricos en la Marina de los EE.UU. y pasó por el servicio de campo y la evaluación de equipos rotativos de todo tipo, desde pequeños a grandes, como Ingeniero Jefe de un gran taller de reparación de motores del Medio Oeste. El Dr. Penrose ha participado directamente en el rebobinado, la formación y la resolución de problemas de equipos de CA, CC, de rotor bobinado, síncronos, de máquinas herramienta y especiales. Sus estudios se centran en la fiabilidad industrial y de los motores eléctricos, los métodos de ensayo, la eficiencia energética y el impacto del mantenimiento en la producción. El Dr. Penrose fue Presidente de la Sección de Chicago del IEEE, Presidente de la Sociedad de Dieléctricos y Aislamiento Eléctrico del IEEE de Chicago, Miembro Profesional de la Asociación de Fabricación Eléctrica de Bobinas y Bobinados, Profesional MotorMaster Certificado por el Departamento de Energía de EE.UU., Analista de Vibraciones, Analista de Infrarrojos y Analista de Circuitos de Motores.