Vantaggi del test del motore CC mediante l’analisi del circuito del motore
Il collaudo elettrico dei motori elettrici a corrente continua (DC) rappresenta una sfida per l’industria, la produzione e i centri di riparazione. Il problema principale riguarda la possibilità di confrontare una bobina con l’altra, nel caso in cui non vengano fornite informazioni precise. In questo articolo si discute la questione dei test semplici per aumentare la fiducia nelle conclusioni dei test e delle analisi utilizzando l’analisi del circuito motore (MCA).
Il termine MCA deriva da un metodo di prova che fornisce informazioni sui componenti di base di un motore elettrico CA o CC. Questi componenti di base comprendono:
- Resistenza, misurata in Ohm
- Impedenza, misurata in Ohm
- Induttanza, misurata in Henries
- L’angolo di fase dell’avvolgimento di induzione, misurato in gradi
- Resistenza di isolamento, misurata in Meg-Ohm
Lo strumento a cui si farà riferimento in questo articolo fornisce queste letture generando un segnale a bassa tensione, a onda sinusoidale vera, a corrente alternata (impedenza, induttanza, angolo di fase), a frequenze comprese tra 100 e 800 hertz, un segnale a bassa tensione in corrente continua per la resistenza e 500 o 1.000 volt in corrente continua per il test della resistenza di isolamento.
Inoltre, viene eseguito un test speciale chiamato I/F in cui la frequenza applicata viene raddoppiata e il rapporto risulta dalla variazione dell’impedenza dell’avvolgimento. Questo test viene introdotto per identificare i primi cortocircuiti che possono verificarsi nell’avvolgimento. Utilizzando i dati applicati, è possibile valutare le condizioni degli avvolgimenti di un motore CC attraverso il confronto delle bobine, il confronto con letture note o l’andamento delle variazioni degli avvolgimenti in un periodo di tempo.
I motori elettrici a corrente continua che verranno trattati in questo articolo sono motori a corrente continua serie, shunt e composti. Alcuni dei test di base descritti possono essere eseguiti su magneti permanenti, servocomandi in c.c., macchine utensili in c.c. e altri (anche se i motori in c.c. senza spazzole vengono valutati in modo simile ai motori in c.a.). I tipi di motori elettrici a corrente continua possono essere descritti in base agli avvolgimenti e ai collegamenti.
Teoria dei motori CC
I motori elettrici a corrente continua funzionano in base a un principio fondamentale dell’elettricità: l’interazione tra due campi magnetici posizionati ad angolo l’uno rispetto all’altro si attraggono e si respingono dando luogo al movimento. Nel caso di un motore elettrico a corrente continua, l’alimentazione viene fornita a un campo statorico e a un’armatura che creano campi magnetici a circa 90 gradi l’uno dall’altro. L’attrazione/repulsione dell’armatura dal campo genera una coppia e l’armatura gira.
I componenti di base di un motore elettrico a corrente continua comprendono:
- Telaio – Costituisce la struttura esterna della macchina. Viene utilizzato per montare la maggior parte degli altri componenti del motore.
- Campi – Si tratta di bobine montate su poli di campo che generano un campo magnetico stazionario.
- Interpoli – Si tratta di bobine collocate tra le bobine di campo che generano un campo utilizzato per prevenire l’eccessiva scintillazione delle spazzole.
- Scudi di estremità – detti anche alloggiamenti dei cuscinetti, sono utilizzati per alloggiare le spazzole e la loro armatura e per ospitare i cuscinetti dell’albero, che mantengono l’armatura centrata nel telaio.
- Sartiame delle spazzole – Sostiene e posiziona le spazzole sopra il commutatore dell’indotto. Di solito si utilizza un dispositivo di tensione per mantenere una pressione costante sulle spazzole.
- Spazzole – Vengono utilizzate per fornire corrente continua all’indotto. Le spazzole si muovono sul commutatore.
- Commutatore – È costituito da numerose barre di rame separate da mica. Ogni barra è collegata alle bobine dell’armatura.
- Armatura – È la parte rotante del motore che contiene le bobine.
A differenza della maggior parte dei motori a corrente alternata, i motori a corrente continua richiedono un’alimentazione separata sia per i campi che per l’indotto. La corrente continua fornita ai campi dello statore genera un insieme costante di campi Nord e Sud. La corrente continua fornita all’armatura genera campi nord e sud che si trovano a 90 gradi elettrici rispetto al campo fisso.
Quando l’indotto genera una coppia e si sposta verso il polo Nord o Sud appropriato, le spazzole cambiano posizione sul commutatore, eccitando un’altra serie di bobine a 90 gradi elettrici dal campo fermo. Ciò rende l’indotto un componente a corrente alternata, in quanto la corrente viaggia in una direzione, in base alla posizione delle spazzole, e poi in un’altra direzione durante il funzionamento del motore.
Le spazzole sono posizionate in modo da essere elettricamente “neutre” (senza corrente indotta dai campi dello statore) per ridurre le scintille. Nella maggior parte dei collegamenti di motori CC, variando la tensione di armatura è possibile modificare la velocità di funzionamento. Un pericolo generale insito nei motori a corrente continua è che se si perde la corrente di campo mentre si mantiene la corrente di armatura, il motore può decollare e la velocità aumenta fino all’autodistruzione dell’armatura.
I tre tipi di avvolgimento di base che possono essere utilizzati per identificare il tipo di motore a corrente continua sono:
- Serie: Normalmente si trovano in applicazioni che richiedono un’elevata coppia di spunto. Sono costituiti da una serie di avvolgimenti di campo a filo largo e con un numero relativamente basso di spire, contrassegnati da S1 e S2, collegati in serie agli interpoli e all’indotto, contrassegnati da A1 e A2 (vedere Figura 1). I motori collegati in serie sono normalmente utilizzati come motori di trazione e presentano una resistenza di base molto bassa.
- Shunt: Normalmente si trova in applicazioni che richiedono una velocità costante. Sono costituiti da una serie di avvolgimenti di campo di filo più piccolo con molte spire, contrassegnati da F1 e F2 per la tensione singola e da F1, F2, F3 e F4 per la doppia tensione, e da A1 e A2 per gli interpoli e l’armatura (vedere le figure 2). I motori collegati in derivazione sono normalmente utilizzati come motori per gru e macchine utensili e presentano una resistenza di base relativamente elevata.
- Composto: Combinano i vantaggi dei motori avvolti in serie e in derivazione. Forniscono una coppia relativamente elevata con una resistenza di base alla variazione della velocità di funzionamento. I collegamenti combinano sia i collegamenti in serie che quelli in derivazione (vedere Figura 3). I motori composti sono i più comuni e si trovano comunemente nella produzione industriale.
Come si può notare, in una macchina a corrente continua assemblata ci sono poche bobine da confrontare tra loro. Tuttavia, è possibile sviluppare procedure per le prove di avvolgimento che garantiscano un elevato livello di affidabilità dei risultati.
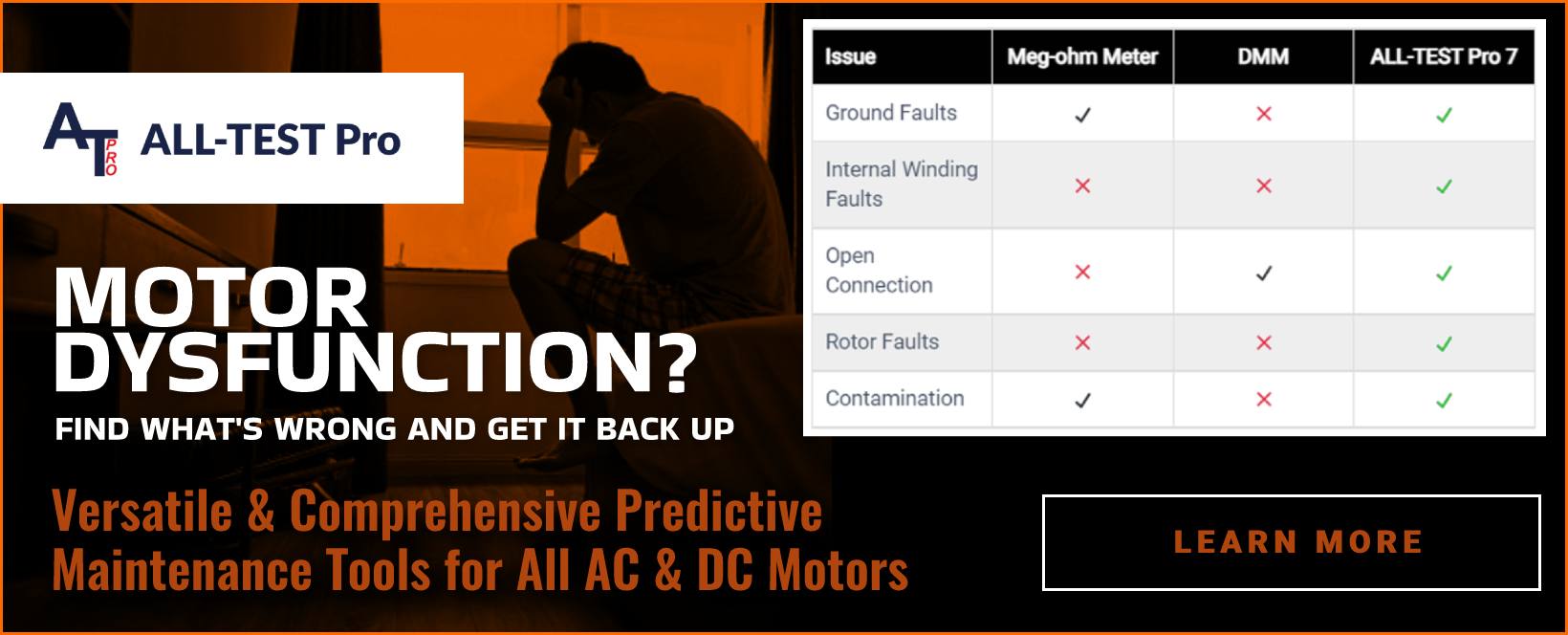
Guasti elettrici comuni dei motori CC
Esiste una serie di guasti elettrici comuni dei motori CC, di cui i più comuni saranno descritti qui di seguito. Questi problemi derivano da problemi specifici della progettazione dei motori CC, dovuti alla temperatura, all’attrito e a contaminanti interni come carbonio o grafite.
Una delle cause più comuni di guasti agli avvolgimenti in un motore CC è la contaminazione degli avvolgimenti da parte di polvere di carbone o grafite (carbonio) proveniente dalle spazzole. La polvere fine permea tutti gli avvolgimenti fissi e rotanti e crea un percorso tra i conduttori o tra i conduttori verso terra. Il carbone è spesso intrappolato e i problemi vengono ulteriormente aggravati dalle pratiche di pulizia e manutenzione quando il carbone viene soffiato con aria compressa o l’armatura viene pulita e cotta. In entrambi i casi, il carbone può diventare stretto negli angoli, di solito dietro il commutatore. Questo si tradurrà in un guasto a terra o in un cortocircuito delle spire proprio sul collegamento del commutatore.
Un altro difetto comune, che spesso non viene considerato, è il raffreddamento della macchina CC. Ciò può verificarsi a causa dell’ostruzione dei passaggi di raffreddamento, della rotazione troppo lenta dell’indotto senza raffreddamento supplementare o della presenza di filtri sporchi (il guasto più comune legato al raffreddamento). La temperatura è il più grande nemico delle apparecchiature elettriche, in particolare del sistema di isolamento, la cui durata si riduce della metà per ogni aumento di 10 gradi centigradi della temperatura (regola empirica accettata). Man mano che l’isolamento si indebolisce, la sua affidabilità diminuisce fino a quando si verificano guasti agli avvolgimenti tra le spire. Oltre al degrado del sistema di isolamento, anche le spazzole si degradano più rapidamente, causando una maggiore usura del commutatore e un’ulteriore contaminazione da carbonio degli avvolgimenti.
Un altro guasto legato al calore è generato da pratiche che hanno i campi eccitati con l’indotto a riposo (diseccitato). Si tratta di una modalità di funzionamento comune che richiede una soffiante separata per fornire il raffreddamento al motore, normalmente dotata di filtri che devono essere mantenuti puliti. Questo tipo di guasto provoca normalmente un cortocircuito delle bobine di derivazione, riducendo la capacità del motore di produrre coppia e, se non viene mantenuto correttamente, può portare alla pericolosa condizione di sovravelocità dell’armatura.
Il commutatore offre inoltre la possibilità di individuare eventuali guasti, nonché un indicatore del funzionamento e delle condizioni del motore. Un motore CC che funziona correttamente presenta una sottile patina di carbonio sul commutatore con le barre uniformi. Barre di commutazione bruciate, vetri striati, carbone pesante o condizioni di surriscaldamento del commutatore indicano problemi potenziali che devono essere affrontati.
Test dell’armatura
Le armature in c.c. sono il componente che richiede più tempo ma più facile da testare. I metodi di base che verranno introdotti sono tre: trending, assemblato e disassemblato. Nel caso del trending, vengono utilizzate tutte le misure, tuttavia, nel caso di test assemblati e smontati, verrà utilizzata una misura di impedenza da barra a barra. L’impedenza viene considerata perché l’armatura è un componente in corrente alternata e le semplici misure di resistenza possono non rilevare alcuni guasti, tra cui i cortocircuiti e le masse. L’andamento sarà esaminato in una procedura di andamento generale per i motori CC più avanti in questo articolo.
Quando si testa un’armatura di un motore CC assemblato, il metodo migliore è quello di eseguire quello che è comunemente noto come test da barra a barra utilizzando le spazzole del motore. Nel caso di un motore a corrente continua con due spazzole, non è necessario sollevare nessuna spazzola, mentre nel caso di un motore a corrente continua con quattro o più gruppi di spazzole, è necessario sollevare tutti i gruppi tranne due a 90 gradi l’uno dall’altro, il che li esclude dal circuito di prova. Assicurarsi che venga mantenuto un buon contatto sul commutatore, verificando che oltre il 90% della spazzola sia a contatto con le barre del commutatore e che queste ultime siano pulite. Se non sono pulite, lucidare delicatamente l’armatura, utilizzando un metodo approvato, prima di eseguire il test. Se il commutatore è molto usurato, dovrà essere smontato e il commutatore dovrà essere “girato e sottoquotato”, nel qual caso sarebbe appropriato un test smontato da barra a barra. Una volta impostata, segnare la posizione di una barra sul commutatore, quindi portare la barra in una posizione in cui si trovi appena sotto il bordo d’attacco di una delle spazzole. Nel test assemblato, probabilmente coprirete almeno una barra e mezza con il pennello. Eseguire un test di impedenza, annotare il valore letto e spostare l’armatura in modo che il bordo anteriore della spazzola si trovi sopra la barra commutatrice successiva. Eseguire la lettura dell’impedenza successiva e continuare fino a testare ogni barra. Un buon risultato mostrerà un modello coerente, mentre un modello incoerente identificherà un’armatura scadente.
Il test da barra a barra smontata è simile a quello montato, con la differenza che l’indotto è fuori dal telaio e il tester ha pieno accesso al commutatore. In questo caso, il tester utilizzerà un’armatura di fissaggio o dei puntali per collegarsi da barra a barra. La distanza tra le letture dell’impedenza deve essere costante e compresa tra 90 e 180 gradi. La prima barra deve essere contrassegnata e il test continua fino a quando una gamba del dispositivo di prova o del puntale non ha compiuto un giro di 360 gradi intorno al commutatore. Segnare l’impedenza per ogni test da barra a barra, quindi verificare che vi sia uno schema coerente.
Test dei motori in serie
I motori elettrici in serie sono molto difficili da risolvere in quanto non forniscono serie di campi da confrontare. Le letture possono essere eseguite da S1 a S2 e da A1 ad A2, per poi essere analizzate nel tempo o confrontate con altre macchine simili.
Quando si esegue il trend delle letture nel tempo, le letture della resistenza semplice devono essere corrette per la temperatura, di solito relativa a 25oC. L’impedenza e l’induttanza normalmente subiscono variazioni limitate a causa della temperatura, mentre l’angolo di fase e le letture I/F rimangono costanti, indipendentemente dalla temperatura. Variazioni nell’I/F e nell’angolo di fase indicano spire in cortocircuito, mentre variazioni nell’impedenza e nell’induttanza indicano normalmente avvolgimenti sporchi.
Il confronto tra motori simili richiede ulteriori informazioni. L’operatore dovrà assicurarsi che il motore sia dello stesso produttore e dello stesso design, oltre che della stessa velocità, potenza, ecc. Il motore “modello” deve essere nuovo o ricostruito secondo le specifiche del produttore originale. Quando si eseguono letture comparative, la temperatura di prova deve essere simile da motore a motore, tuttavia le letture I/F e dell’angolo di fase possono essere confrontate direttamente. Queste letture non devono cambiare più di +/- 2 punti per I/F e +/-1 grado per l’angolo di fase. Un errore comune quando si ricostruiscono gli avvolgimenti di campo in serie, anche se meno comune rispetto alle bobine shunt, è la sostituzione errata delle dimensioni dei fili, che influisce sulla capacità del motore di generare coppia.
Test del motore shunt
I motori shunt a doppia tensione consentono di confrontare due serie di avvolgimenti, mentre per i motori a tensione singola si applica la stessa procedura di prova degli avvolgimenti dei motori in serie, utilizzando F1 e F2 anziché S1 e S2.
Con la doppia tensione, gli avvolgimenti shunt sono etichettati da F1 a F2 e da F3 a F4, consentendo all’analista di testare e confrontare queste due serie di avvolgimenti.
Durante i test e la risoluzione dei problemi, le letture della resistenza semplice devono essere corrette in base alla temperatura, di solito relativa a 25oC. L’impedenza e l’induttanza cambieranno maggiormente rispetto a un motore avvolto in serie a causa della maggiore resistenza semplice del circuito. L’angolo di fase e l’I/F rimarranno costanti, entro 1 o 2 punti, indipendentemente dalla temperatura. Variazioni nell’I/F e nell’angolo di fase indicano spire in cortocircuito, mentre variazioni nell’impedenza e nell’induttanza indicano normalmente avvolgimenti sporchi. I confronti tra F1 e F2 e tra F3 e F4 devono essere inferiori al 3% per quanto riguarda la resistenza, l’induttanza e l’impedenza e non più di un punto di differenza per quanto riguarda l’I/F o l’angolo di fase.
I motori “like” possono essere testati e confrontati come i motori avvolti in serie. Quando è possibile, i motori devono essere testati, quando si verificano le letture di tendenza, alla stessa temperatura dei test precedenti. Ad esempio, entro pochi minuti dallo spegnimento dell’apparecchiatura in funzione o prima dell’avvio dell’apparecchiatura, questo consente di eseguire i test a temperature simili.
Test del motore CC composto
I test in loco, le tendenze e la risoluzione dei problemi sono molto più semplici con un motore composto. I motori composti a tensione singola sono normalmente etichettati da A1 ad A2, da S1 a S2 e da F1 a F2, mentre i motori composti a doppia tensione sono normalmente etichettati da A1 ad A2, da S1 a S2, da F1 a F2 e da F3 a F4. Un altro aspetto fondamentale di un motore a avvolgimento composto è che l’avvolgimento in serie è normalmente avvolto sopra l’avvolgimento in derivazione, consentendo eventuali guasti tra questi due avvolgimenti.
In caso di motori composti, i test vengono normalmente eseguiti sui terminali dell’azionamento CC. I test MCA standard che utilizzano l’ALL-TEST comportano segnali a bassa tensione e ad alta frequenza che non danneggiano l’elettronica di uscita dell’apparecchiatura, riducendo la necessità di scollegare i cavi dall’azionamento durante il test. Tuttavia, se l’analista desidera verificare la resistenza di isolamento tra gli avvolgimenti serie e shunt, i conduttori devono essere scollegati dall’azionamento. Quando si esegue il trend dal convertitore di frequenza, testare A1 a S2 e i due conduttori di campo, quindi eseguire un test di resistenza di isolamento a 500 Volt tra i conduttori S2 e F1 e confrontare con i test precedenti o con motori simili; in entrambi i casi, le letture della resistenza di isolamento devono rimanere superiori a 100 Meg-Ohm.
L’unità ALL-TEST consente all’analizzatore di confrontare immediatamente le letture passate con quelle attuali per un rapido controllo, consentendo all’analizzatore di prendere una rapida decisione di testare ulteriormente gli avvolgimenti. Come indicato nelle tecniche di test dei motori in serie e in derivazione, le letture dell’I/F e dell’angolo di fase non dovrebbero cambiare di più di un punto tra un test e l’altro; tuttavia, con il passare del tempo, gli avvolgimenti di serie e di campo varieranno notevolmente l’uno dall’altro.
La ricerca dei guasti sui motori composti deve essere effettuata sul motore stesso. Scollegare tutti i cavi del motore e separarli. Testare gli avvolgimenti di serie e di campo come indicato nelle istruzioni per gli avvolgimenti di serie e di derivazione, quindi eseguire un test della resistenza di isolamento tra gli avvolgimenti di serie e di derivazione; la resistenza di isolamento deve essere superiore a 100 Meg-Ohm.
Note sui test dei motori CC MCA
Il test MCA su qualsiasi tipo di motore a corrente continua consente di ottenere diversi punti chiave:
- Qualsiasi lettura I/F al di fuori dell’intervallo tra -15 e -50, ad esempio -56, indica un guasto all’avvolgimento.
- Se il test mostra una resistenza infinita tra i conduttori dello stesso circuito, indica un avvolgimento aperto.
- Un aumento della resistenza semplice tra i test, se corretto per la temperatura, indica un collegamento allentato, in particolare quando le letture di impedenza e induttanza cambiano. Una resistenza semplice ridotta, se corretta per la temperatura, può indicare un cortocircuito, di solito accompagnato da variazioni dell’impedenza, dell’induttanza, dell’angolo di fase e dell’I/F.
- Quando si eseguono test come i motori, l’I/F e l’angolo di fase non dovrebbero cambiare più di 2 punti; qualsiasi differenza superiore a questa dovrebbe richiedere un’analisi completa.
- I cambiamenti durante il test attraverso il circuito dell’armatura dovrebbero richiedere un test da barra a barra.
Seguendo queste semplici istruzioni, l’uso di un dispositivo MCA consente di individuare i guasti precoci molto prima che l’apparecchiatura si guasti durante il funzionamento. Se si eseguono i test come parte di un programma di manutenzione predittiva, l’intervallo deve essere almeno quello indicato nella Tabella 1.
Tabella 1: Frequenza di prova del motore CC
Tipo di test | Non critico | Generale | Critico |
Manutenzione generale | 1 anno | 6-9 mesi | 3-6 mesi |
Manutenzione predittiva | 6 mesi | 3 mesi | 1 mese |
Test dell’armatura | 1 anno | 6 mesi | 3 mesi |
I test di manutenzione generale sono quelli che non hanno un trend nel tempo. Di solito è accompagnata da vibrazioni, ingrassaggio dei cuscinetti, ispezione del commutatore e delle spazzole. I test di manutenzione predittiva normalmente prevedono l’andamento delle letture nel tempo per individuare potenziali guasti e determinare il momento migliore per rimuovere il motore per la manutenzione correttiva. Una volta rilevato un potenziale guasto, la frequenza dei test deve aumentare fino a quando non si stabilisce che il motore deve essere rimosso. Un test completo dell’indotto dovrebbe essere eseguito insieme a un test di manutenzione generale o predittivo a causa delle elevate sollecitazioni sul commutatore e della contaminazione da carbone.
Conclusione
La verifica elettrica generale dei motori elettrici a corrente continua è resa molto più semplice dalle nuove tecniche disponibili con l’analisi statica dei circuiti del motore. Per la prima volta, è possibile rilevare precocemente i guasti di rotazione negli avvolgimenti di serie, derivazione e armatura prima che mettano fuori uso le apparecchiature. I test di manutenzione preventiva possono essere eseguiti dal convertitore di frequenza, mentre i test di ricerca guasti vengono eseguiti sul motore. In generale, i test sono relativamente rapidi e richiedono meno di cinque minuti per motore per i test di manutenzione predittiva, con un tempo aggiuntivo per la risoluzione dei problemi. Nel complesso, il test MCA migliora notevolmente il test dei motori CC rispetto ai metodi tradizionali di test di continuità.
Sull’autore
Howard W. Penrose, Ph.D., lavora da oltre 15 anni nel settore dei motori elettrici e della loro riparazione. Da tecnico riparatore di motori elettrici nella Marina Militare degli Stati Uniti, è passato all’assistenza sul campo e alla valutazione di apparecchiature rotanti di tutti i tipi, da piccole a grandi, come ingegnere capo di una grande officina di riparazione motori del Midwest. Il Dr. Penrose è stato direttamente coinvolto nel riavvolgimento, nella formazione e nella ricerca guasti di apparecchiature CA, CC, a rotore avvolto, sincrone, macchine utensili e speciali. I suoi studi riguardano l’affidabilità dei motori elettrici e industriali, i metodi di prova, l’efficienza energetica e l’impatto della manutenzione sulla produzione. Penrose è un ex presidente della sezione di Chicago dell’IEEE, un ex presidente della Dielectrics and Electrical Insulation Society dell’IEEE di Chicago, un membro professionista dell’Electrical Manufacturing Coil and Winding Association, un professionista MotorMaster certificato dal Dipartimento dell’Energia degli Stati Uniti, un analista delle vibrazioni, un analista degli infrarossi e un analista dei circuiti motore.