Zalety testu silnika DC z wykorzystaniem analizy obwodu silnika
Testy elektryczne silników elektrycznych prądu stałego (DC) stanowią wyzwanie zarówno w przemyśle, produkcji, jak i centrach naprawczych. Kluczową kwestią jest możliwość porównania jednej cewki z drugą, w przypadku braku dokładnych informacji. W tym artykule omówiono kwestię prostych testów w celu zwiększenia pewności wniosków z testów i analiz przy użyciu analizy obwodów silnika (MCA).
Termin MCA pochodzi od metody testowej, która dostarcza informacji na temat podstawowych komponentów silnika elektrycznego AC lub DC. Te podstawowe komponenty obejmują:
- Rezystancja, mierzona w omach
- Impedancja, mierzona w omach
- Indukcyjność, mierzona w Henriach
- Kąt fazowy uzwojenia indukcyjnego, mierzony w stopniach
- Rezystancja izolacji, mierzona w Meg-Ohmach
Przyrząd, o którym będzie mowa w tym artykule, zapewnia te odczyty poprzez generowanie niskonapięciowego, prawdziwie sinusoidalnego, prądu przemiennego (impedancja, indukcyjność, kąt fazowy), sygnału o częstotliwości od 100 do 800 Hz, niskonapięciowego sygnału DC dla rezystancji oraz 500 lub 1000 woltów DC dla testu rezystancji izolacji.
Ponadto wykonywany jest specjalny test o nazwie I/F, w którym stosowana częstotliwość jest podwajana, a stosunek wynika ze zmiany impedancji uzwojenia. Ten test jest wprowadzany w celu identyfikacji wczesnych zwarć uzwojenia, które mogą występować w uzwojeniu. Korzystając z zastosowanych danych, stan uzwojenia silnika prądu stałego można ocenić poprzez porównanie cewek, porównanie ze znanymi odczytami lub poprzez trend zmian uzwojeń w danym okresie czasu.
Silniki elektryczne prądu stałego, które zostaną uwzględnione w tym artykule, to szeregowe, bocznikowe i złożone silniki prądu stałego. Niektóre z opisanych podstawowych testów można przeprowadzić na magnesach trwałych, serwomechanizmach DC, obrabiarkach DC i innych (chociaż bezszczotkowe silniki DC są oceniane w podobny sposób jak silniki AC). Typy silników elektrycznych prądu stałego można opisać za pomocą ich uzwojeń i połączeń.
Teoria silników prądu stałego
Silniki elektryczne prądu stałego działają zgodnie z podstawową zasadą elektryczności: interakcja między dwoma polami magnetycznymi umieszczonymi pod kątem względem siebie przyciąga/odpycha, powodując ruch. W przypadku silnika elektrycznego prądu stałego, moc jest dostarczana do pola stojana i twornika tworzących pola magnetyczne, które elektrycznie są oddalone od siebie o około 90 stopni. Wynikające z tego przyciąganie/odpychanie twornika od pola generuje moment obrotowy i twornik obraca się.
Podstawowe komponenty silnika elektrycznego DC obejmują:
- Rama – tworzy zewnętrzną strukturę urządzenia. Służy on do montażu większości innych komponentów silnika
- Pola – są to cewki zamontowane na nabiegunnikach, które generują stacjonarne pole magnetyczne.
- Interpole – są to cewki umieszczone pomiędzy cewkami pola, które generują pole wykorzystywane do zapobiegania nadmiernemu iskrzeniu szczotek.
- Endshieldy – nazywane również obudowami łożysk, są używane do umieszczania szczotek i olinowania szczotek oraz do umieszczania łożysk wału, utrzymując armaturę wyśrodkowaną w ramie.
- Olinowanie szczotek – utrzymuje i pozycjonuje szczotki nad komutatorem twornika. Zazwyczaj do utrzymania stałego nacisku na szczotki stosuje się urządzenie napinające.
- Szczotki – służą do dostarczania prądu stałego do twornika. Szczotki poruszają się po komutatorze.
- Komutator – składa się z wielu miedzianych prętów oddzielonych miką. Każdy pręt jest podłączony do cewek w tworniku.
- Armatura – jest to obracająca się część silnika, która zawiera cewki.
W przeciwieństwie do większości silników prądu przemiennego, silniki prądu stałego wymagają oddzielnego zasilania pól i twornika. Prąd stały dostarczany do pól stojana generuje stały zestaw pól północnych i południowych. Prąd stały dostarczany do twornika generuje pola północne i południowe, które są oddalone o 90 stopni elektrycznych od pola stacjonarnego.
Gdy zwora generuje moment obrotowy i porusza się w kierunku odpowiedniego bieguna północnego lub południowego, szczotki zmieniają położenie na komutatorze, zasilając inny zestaw cewek o 90 stopni elektrycznych od stacjonarnego pola. W rzeczywistości sprawia to, że twornik jest elementem prądu przemiennego, ponieważ prąd będzie płynął w jednym kierunku, w zależności od położenia szczotki, a następnie w innym kierunku podczas pracy silnika.
Szczotki są ustawione w takiej pozycji, aby były elektrycznie “neutralne” (brak prądu indukowanego z pól stojana) w celu ograniczenia iskrzenia. W większości połączeń silników prądu stałego, zmieniając napięcie twornika, można zmienić prędkość roboczą. Jednym z ogólnych zagrożeń związanych z silnikami prądu stałego jest to, że jeśli prąd pola zostanie utracony, podczas gdy prąd twornika jest utrzymywany, silnik może wystartować, a prędkość wzrasta aż do samozniszczenia twornika.
Trzy podstawowe typy uzwojeń, które można wykorzystać do identyfikacji typu silnika prądu stałego, to:
- Seria: Zwykle stosowane w aplikacjach wymagających wysokiego momentu rozruchowego. Składają się one z zestawu uzwojeń polowych z dużego drutu i stosunkowo niewielu zwojów, oznaczonych S1 i S2, które są połączone szeregowo z biegunami pośrednimi i twornikiem, oznaczonymi A1 i A2 (patrz rysunek 1). Silniki połączone szeregowo są zwykle używane jako silniki trakcyjne i mają bardzo niską rezystancję podstawową.
- Bocznik: Zwykle spotykany w aplikacjach wymagających stałej prędkości. Składają się one z zestawu uzwojeń polowych z mniejszego drutu o wielu zwojach, oznaczonych F1 i F2 dla pojedynczego napięcia oraz F1, F2, F3 i F4 dla podwójnego napięcia, a także A1 i A2 dla biegunów pośrednich i twornika (patrz rysunek 2). Silniki bocznikowe są zwykle używane jako silniki dźwigów i obrabiarek i mają stosunkowo wysoką rezystancję podstawową.
- Złożony: Łączą zalety silników z uzwojeniem szeregowym i bocznikowym. Zapewniają one stosunkowo wysoki moment obrotowy przy podstawowej odporności na zmianę prędkości roboczej. Połączenia łączą zarówno połączenia szeregowe, jak i bocznikowe (patrz rysunek 3). Silniki zespolone są najczęściej spotykane w produkcji przemysłowej.
Jak widać, w zmontowanej maszynie DC jest niewiele cewek, które można ze sobą porównać. Można jednak opracować procedury testowania uzwojenia, które zapewniają wysoki poziom pewności wyników testu.
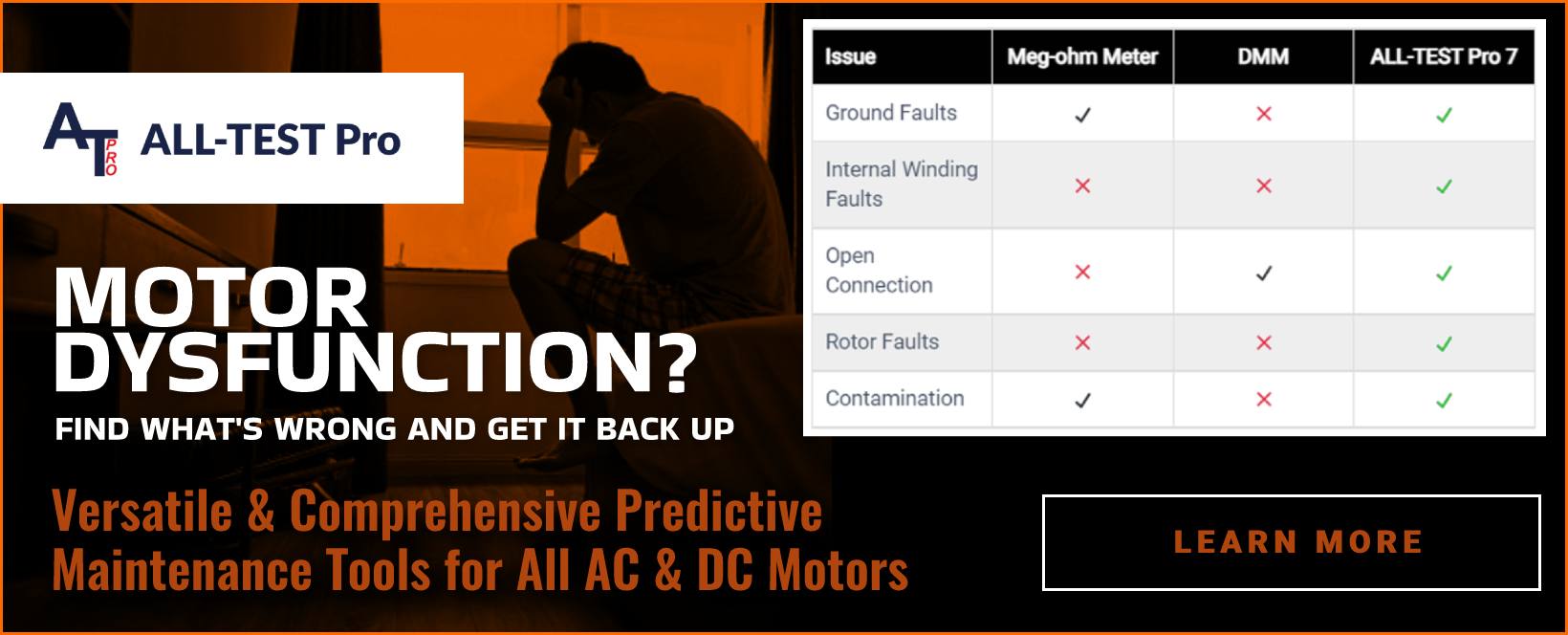
Typowe usterki elektryczne silnika prądu stałego
Istnieje wiele typowych usterek elektrycznych silnika prądu stałego, z których najczęstsze zostaną opisane tutaj. Wynikają one z kwestii specyficznych dla konstrukcji silnika prądu stałego w wyniku temperatury, tarcia i wewnętrznych zanieczyszczeń, takich jak węgiel lub grafit.
Jedną z najczęstszych przyczyn usterek uzwojenia w silniku prądu stałego jest zanieczyszczenie uzwojenia pyłem węglowym lub grafitowym (węglowym) ze szczotek. Drobny proszek przenika wszystkie uzwojenia stacjonarne i obrotowe i tworzy ścieżkę między przewodnikami lub między przewodnikami a uziemieniem. Węgiel jest często uwięziony, a problemy pogarszają się jeszcze bardziej podczas czyszczenia i konserwacji, gdy węgiel jest przedmuchiwany sprężonym powietrzem lub armatura jest czyszczona i wypalana. W obu przypadkach węgiel może zostać ciasno upakowany w rogach, zwykle tuż za komutatorem. Zakończy się to zwarciem doziemnym lub zwarciem zwojów bezpośrednio na połączeniu komutatora.
Inną częstą usterką, która często nie jest brana pod uwagę, jest chłodzenie maszyny DC. Może to wynikać z zablokowania kanałów chłodzących, zbyt wolnego obracania twornika bez dodatkowego chłodzenia lub z zabrudzenia filtrów (najczęstsza usterka związana z chłodzeniem). Temperatura jest największym wrogiem sprzętu elektrycznego, w szczególności systemu izolacji, którego żywotność skraca się o połowę na każde 10 stopni Celsjusza wzrostu temperatury (przyjęta zasada). W miarę jak izolacja słabnie, jej niezawodność spada, aż do wystąpienia usterek uzwojenia między zwojami. Oprócz degradacji systemu izolacji, szczotki również ulegają szybszej degradacji, powodując zwiększone zużycie komutatora i dodatkowe zanieczyszczenie uzwojeń węglem.
Inna usterka związana z ciepłem jest generowana przez praktyki, w których pola są pod napięciem, a zwora jest w stanie spoczynku (odłączona od napięcia). Jest to powszechny tryb pracy, który wymaga oddzielnej dmuchawy, aby zapewnić chłodzenie silnika, który zwykle ma filtry, które muszą być utrzymywane w czystości. Ten typ usterki zwykle powoduje zwarcie cewek bocznikowych, zmniejszając zdolność silnika do wytwarzania momentu obrotowego, a jeśli nie jest odpowiednio konserwowany, może zakończyć się niebezpiecznym stanem nadmiernej prędkości twornika.
Komutator zapewnia również możliwość wykrycia usterek, a także wskaźnik działania i stanu silnika. Prawidłowo działający silnik prądu stałego będzie miał cienką warstwę węgla na komutatorze, a pręty będą wyglądały jednolicie. Przepalone pręty komutatora, smugi na szkle, duża ilość węgla lub przegrzany komutator wskazują na potencjalne problemy, którymi należy się zająć.
Testowanie armatury
Armatura DC jest najbardziej czasochłonnym, ale najłatwiejszym do przetestowania komponentem. Istnieją trzy podstawowe metody, które zostaną wprowadzone: trendowanie, montaż i demontaż. W przypadku trendów używane są wszystkie pomiary, jednak w przypadku testów zmontowanych i zdemontowanych używany jest pomiar impedancji między prętami. Impedancja jest brana pod uwagę, ponieważ twornik jest elementem prądu przemiennego, a proste pomiary rezystancji mogą pomijać niektóre usterki, w tym zwarcia i uziemienia. Trendy zostaną omówione w ogólnej procedurze trendowania dla silników prądu stałego w dalszej części tego artykułu.
Podczas testowania zmontowanej twornika silnika prądu stałego, najlepszą metodą jest wykonanie tak zwanego testu pręt-pręt przy użyciu szczotek silnika. W przypadku silnika prądu stałego, który ma dwie szczotki, żadna ze szczotek nie musi być podniesiona, w przypadku silnika prądu stałego, który ma cztery lub więcej zestawów szczotek, wszystkie oprócz dwóch zestawów 90 stopni od siebie muszą być podniesione, co wyłącza je z obwodu testowego. Upewnij się, że na komutatorze utrzymywany jest dobry kontakt, upewniając się, że ponad 90% szczotki styka się z prętami komutatora i że pręty komutatora są czyste. Jeśli nie są one czyste, przed testowaniem należy delikatnie wypolerować armaturę przy użyciu zatwierdzonej metody. Jeśli komutator jest mocno zużyty, należy go zdemontować, a komutator “obrócić i podciąć”, w którym to przypadku odpowiedni będzie zdemontowany test pręt-pręt. Po ustawieniu zaznacz pozycję jednego pręta na komutatorze, a następnie ustaw pręt w pozycji, w której znajduje się tuż pod krawędzią prowadzącą jednej ze szczotek. W zmontowanym teście prawdopodobnie pokryjesz pędzlem co najmniej półtora paska. Wykonaj test impedancji, zanotuj odczyt i przesuń twornik tak, aby przednia krawędź szczotki znalazła się nad następnym prętem komutatora. Dokonaj kolejnego odczytu impedancji i kontynuuj do momentu przetestowania każdego paska. Dobry wynik pokaże spójny wzór, podczas gdy niespójny wzór zidentyfikuje słabą armaturę.
Testowanie zdemontowanego pręta jest podobne do testowania zmontowanego, z tą różnicą, że twornik znajduje się poza ramą, a tester ma pełny dostęp do komutatora. W takim przypadku tester użyje uchwytu twornika lub przewodów pomiarowych do połączenia między prętami. Odstępy między poszczególnymi odczytami impedancji powinny być stałe i wynosić około 90 do 180 stopni od siebie. Należy zaznaczyć pierwszy pręt i kontynuować testowanie, aż jedna noga urządzenia testującego lub przewodu testowego wykona 360 stopni wokół komutatora. Oznacz impedancję dla każdego testu bar-to-bar, a następnie sprawdź, czy występuje spójny wzorzec.
Seryjne testowanie silników
Seryjne silniki elektryczne są bardzo trudne w rozwiązywaniu problemów, ponieważ nie zapewniają zestawów pól do porównania. Odczyty mogą być pobierane z S1 do S2 i A1 do A2, a następnie trendowane w czasie lub porównywane z innymi podobnymi urządzeniami.
Podczas śledzenia trendów odczytów w czasie, proste odczyty rezystancji muszą być skorygowane o temperaturę, zwykle w odniesieniu do 25oC. Impedancja i indukcyjność zwykle mają ograniczone zmiany ze względu na temperaturę, podczas gdy kąt fazowy i odczyty I/F pozostaną stałe, niezależnie od temperatury. Zmiany I/F i kąta fazowego będą wskazywać na zwarte zwoje, podczas gdy zmiany impedancji i indukcyjności będą zwykle wskazywać na zanieczyszczone uzwojenia.
Porównanie podobnych silników będzie wymagało dodatkowych informacji. Operator będzie musiał upewnić się, że silnik jest tego samego producenta i ma taką samą konstrukcję, a także prędkość, moc itp. Silnik “modelowy” musi być nowy lub przebudowany zgodnie z oryginalnymi specyfikacjami producenta. Podczas wykonywania odczytów porównawczych temperatura testowania powinna być podobna dla każdego silnika, jednak odczyty I/F i kąta fazowego mogą być porównywane bezpośrednio. Odczyty te nie powinny zmieniać się o więcej niż +/- 2 punkty dla I/F i +/-1 stopień dla kąta fazowego. Częstym błędem podczas przebudowy uzwojeń szeregowych, choć mniej powszechnym niż w przypadku cewek bocznikowych, jest nieprawidłowa wymiana rozmiaru drutu, co wpłynie na zdolność silnika do generowania momentu obrotowego.
Testowanie silników bocznikowych
Dwunapięciowe silniki bocznikowe zapewniają możliwość porównania dwóch zestawów uzwojeń, podczas gdy silniki jednonapięciowe będą miały tę samą procedurę testową, co testowanie uzwojeń silnika szeregowego, przy użyciu F1 do F2 w przeciwieństwie do S1 do S2.
W przypadku podwójnego napięcia uzwojenia bocznika są oznaczone od F1 do F2 i od F3 do F4, co pozwala analitykowi przetestować i porównać te dwa zestawy uzwojeń.
Podczas testowania i rozwiązywania problemów z odczytami w czasie, proste odczyty rezystancji muszą być skorygowane o temperaturę, zwykle w odniesieniu do 25oC. Impedancja i indukcyjność zmienią się bardziej niż w przypadku silnika z uzwojeniem szeregowym ze względu na wyższą prostą rezystancję obwodu. Kąt fazowy i I/F pozostaną stałe, w zakresie od 1 do 2 punktów, niezależnie od temperatury. Zmiany I/F i kąta fazowego będą wskazywać na zwarte zwoje, podczas gdy zmiany impedancji i indukcyjności będą zwykle wskazywać na zanieczyszczone uzwojenia. Porównania między F1 a F2 i F3 a F4 powinny być mniejsze niż 3% w rezystancji, indukcyjności i impedancji oraz nie więcej niż 1 punkt różnicy w I/F lub kącie fazowym.
Podobne silniki mogą być testowane i porównywane tak samo jak silniki z uzwojeniem szeregowym. Jeśli to możliwe, silniki powinny być testowane w tej samej temperaturze, co poprzednie testy. Na przykład, w ciągu kilku minut od wyłączenia działającego sprzętu lub przed uruchomieniem sprzętu, pozwala to na przeprowadzenie testów w podobnych temperaturach.
Test złożonego silnika prądu stałego
Testowanie na miejscu, śledzenie trendów i rozwiązywanie problemów jest znacznie prostsze w przypadku silnika złożonego. Silniki jednonapięciowe są zwykle oznaczone jako A1 do A2, S1 do S2 i F1 do F2, a silniki dwunapięciowe są zwykle oznaczone jako A1 do A2, S1 do S2, F1 do F2 i F3 do F4. Kluczowym dodatkowym punktem silnika z uzwojeniem złożonym jest to, że uzwojenie szeregowe jest zwykle nawinięte na uzwojeniu bocznikowym, co pozwala na ewentualne usterki między tymi dwoma uzwojeniami.
W przypadku silników złożonych testy są zwykle wykonywane z zacisków napędu prądu stałego. Standardowe testy MCA przy użyciu ALL-TEST obejmują sygnały o niskim napięciu i wyższej częstotliwości, które nie uszkodzą wyjściowej elektroniki sprzętu, zmniejszając potrzebę odłączania przewodów od napędu podczas testowania. Jeśli jednak analityk chce sprawdzić rezystancję izolacji między uzwojeniami szeregowymi i bocznikowymi, przewody muszą być odłączone od przemiennika. Podczas śledzenia trendów z napędu DC, przetestuj A1 do S2 i dwa przewody polowe, a następnie wykonaj test rezystancji izolacji 500 V między przewodami S2 i F1 i porównaj z poprzednimi testami lub podobnymi silnikami, w obu przypadkach odczyty rezystancji izolacji powinny pozostać powyżej 100 Meg-Ohmów.
Jednostka ALL-TEST umożliwia analizatorowi natychmiastowe porównanie przeszłych i obecnych odczytów w celu szybkiego sprawdzenia, co pozwala analizatorowi na podjęcie szybkiej decyzji o dalszym testowaniu uzwojeń. Jak wspomniano w technikach testowania silników szeregowych i bocznikowych, odczyty I/F i kąta fazowego nie powinny zmieniać się o więcej niż 1 punkt między testami, jednak z czasem uzwojenia szeregowe i polowe będą się od siebie znacznie różnić.
Rozwiązywanie problemów z silnikami złożonymi powinno odbywać się przy samym silniku. Odłącz wszystkie przewody silnika i rozdziel je. Przetestuj uzwojenia szeregowe i polowe zgodnie z instrukcjami dotyczącymi uzwojeń szeregowych i bocznikowych, a następnie wykonaj test rezystancji izolacji między uzwojeniami szeregowymi i bocznikowymi, rezystancja izolacji powinna być większa niż 100 megaomów.
Uwagi dotyczące testowania silników prądu stałego MCA
Za pomocą testów MCA na dowolnym typie silnika prądu stałego można określić kilka kluczowych punktów:
- Każdy odczyt I/F poza zakresem od -15 do -50, na przykład -56, wskazuje na usterkę uzwojenia.
- Jeśli test wykaże nieskończoną rezystancję między przewodami tego samego obwodu, oznacza to otwarte uzwojenie.
- Wzrost prostej rezystancji między testami, po skorygowaniu o temperaturę, wskazuje na luźne połączenie, w szczególności gdy zmieniają się odczyty impedancji i indukcyjności. Zmniejszona rezystancja prosta, po skorygowaniu o temperaturę, może wskazywać na zwarcie, któremu zwykle towarzyszą zmiany impedancji, indukcyjności, kąta fazowego i I/F.
- Podczas testowania takich silników, I/F i kąt fazowy nie powinny zmieniać się o więcej niż 2 punkty, każda różnica większa niż ta powinna spowodować pełną analizę.
- Zmiany zachodzące podczas testowania obwodu twornika powinny skłonić do przeprowadzenia testu pręt-pręt.
Postępując zgodnie z tymi prostymi instrukcjami, korzystanie z urządzenia MCA pozwoli na wychwycenie wczesnych usterek na długo przed awarią sprzętu podczas pracy. W przypadku przeprowadzania testów w ramach programu konserwacji zapobiegawczej, odstępy czasu powinny być co najmniej takie, jak pokazano w tabeli 1.
Tabela 1: Częstotliwość testu silnika prądu stałego
Typ testu | Niekrytyczne | Ogólne | Krytyczny |
Ogólna konserwacja | 1 rok | 6-9 miesięcy | 3-6 miesięcy |
Konserwacja predykcyjna | 6 miesięcy | 3 miesiące | 1 miesiąc |
Test armatury | 1 rok | 6 miesięcy | 3 miesiące |
Ogólne testy konserwacyjne to te, które nie podlegają trendom w czasie. Zwykle towarzyszą temu wibracje, smarowanie łożysk, kontrola komutatora i kontrola szczotek. Testowanie konserwacji predykcyjnej zwykle obejmuje trendowanie odczytów w czasie w celu wykrycia potencjalnych usterek, a następnie określenie najlepszego czasu na demontaż silnika w celu przeprowadzenia konserwacji naprawczej. Po wykryciu potencjalnej usterki częstotliwość testowania powinna wzrosnąć do momentu stwierdzenia, że silnik wymaga demontażu. Kompletny test twornika powinien być przeprowadzony w połączeniu z ogólnym lub predykcyjnym testem konserwacyjnym ze względu na wysokie naprężenia w komutatorze i zanieczyszczenie węglem.
Wniosek
Ogólne testy elektryczne silników elektrycznych prądu stałego są znacznie łatwiejsze dzięki nowym technikom dostępnym w statycznej analizie obwodu silnika. Po raz pierwszy możliwe jest wczesne wykrywanie usterek w uzwojeniach szeregowych, bocznikowych i twornika, zanim spowodują one wyłączenie sprzętu z eksploatacji. Testy konserwacji zapobiegawczej mogą być wykonywane z poziomu przemiennika, a testy wykrywania i usuwania usterek mogą być przeprowadzane na silniku. Ogólnie rzecz biorąc, testy są stosunkowo szybkie, wymagając mniej niż pięciu minut na silnik w przypadku testów konserwacji predykcyjnej, z dodatkowym czasem wymaganym na rozwiązywanie problemów. Ogólnie rzecz biorąc, testy MCA znacznie usprawniają testowanie silników prądu stałego w porównaniu z tradycyjnymi metodami testów ciągłości.
O autorze
Dr Howard W. Penrose ma ponad 15 lat doświadczenia w branży silników elektrycznych i ich napraw. Począwszy od czeladnika naprawy silników elektrycznych w Marynarce Wojennej Stanów Zjednoczonych, po serwis terenowy i ocenę małych i dużych urządzeń obrotowych wszystkich typów, jako główny inżynier dużego warsztatu naprawy silników na Środkowym Zachodzie. Dr Penrose był bezpośrednio zaangażowany w przewijanie, szkolenie i rozwiązywanie problemów z AC, DC, wirnikiem nawijanym, synchronicznym, obrabiarkami i specjalistycznym sprzętem. Jego dalsze badania dotyczą niezawodności silników elektrycznych i przemysłowych, metod testowania, efektywności energetycznej i wpływu konserwacji na produkcję. Dr Penrose jest byłym przewodniczącym Sekcji Chicago IEEE, byłym przewodniczącym Dielectrics and Electrical Insulation Society of IEEE Chicago, profesjonalnym członkiem Electrical Manufacturing Coil and Winding Association, certyfikowanym przez Departament Energii USA specjalistą MotorMaster, analitykiem wibracji, analitykiem podczerwieni i analitykiem obwodów silnikowych.