Avantages de l’essai des moteurs à courant continu grâce à l’analyse des circuits des moteurs
Le contrôle électrique des moteurs électriques à courant continu (CC) est un défi pour l’industrie, la fabrication et les centres de réparation. La question essentielle concerne la possibilité de comparer une bobine à une autre, si des informations exactes ne sont pas fournies. Dans cet article, la question des tests simples pour augmenter la confiance des conclusions des tests et des analyses utilisant l’analyse des circuits du moteur (MCA) sera abordée.
Le terme MCA est dérivé d’une méthode d’essai qui fournit des informations sur les composants de base d’un moteur électrique à courant alternatif ou continu. Ces éléments de base sont les suivants
- Résistance, mesurée en Ohms
- Impédance, mesurée en Ohms
- Inductance, mesurée en Henries
- Angle de phase de l’enroulement d’induction, mesuré en degrés
- Résistance d’isolation, mesurée en Meg-Ohms
L’instrument auquel il sera fait référence dans cet article fournit ces relevés en générant un signal basse tension, sinusoïdal, de courant alternatif (impédance, inductance, angle de phase), à des fréquences de 100 à 800 hertz, un signal basse tension en courant continu pour la résistance, et 500 ou 1 000 volts en courant continu pour le test de résistance d’isolement.
En outre, un test spécial appelé I/F est effectué dans lequel la fréquence appliquée est doublée et un rapport résulte du changement de l’impédance de l’enroulement. Ce test est introduit pour identifier les courts-circuits précoces qui peuvent exister dans le bobinage. En utilisant les données appliquées, l’état d’un enroulement de moteur à courant continu peut être évalué par des comparaisons de bobines, des comparaisons à des lectures connues, ou par des tendances de changements des enroulements sur une période de temps.
Les moteurs électriques à courant continu dont il est question dans cet article sont les moteurs à courant continu en série, les moteurs à courant continu shunt et les moteurs à courant continu composés. Certains des tests de base décrits peuvent être effectués sur des aimants permanents, des servomoteurs à courant continu, des machines-outils à courant continu et autres (bien que les moteurs à courant continu sans balais soient évalués de la même manière que les moteurs à courant alternatif). Les types de moteurs électriques à courant continu peuvent être décrits par leurs enroulements et leurs connexions.
Théorie des moteurs à courant continu
Les moteurs électriques à courant continu fonctionnent selon un principe de base de l’électricité : l’interaction entre deux champs magnétiques positionnés à un angle l’un par rapport à l’autre s’attire/se repousse, ce qui entraîne un mouvement. Dans le cas d’un moteur électrique à courant continu, l’énergie est fournie à un champ de stator et à un induit créant des champs magnétiques qui sont, électriquement, à environ 90 degrés l’un de l’autre. L’attraction/répulsion de l’armature par rapport au champ qui en résulte génère un couple et l’armature tourne.
Les composants de base d’un moteur électrique à courant continu sont les suivants :
- Cadre – Constitue la structure extérieure de la machine. Il est utilisé pour monter la plupart des autres composants du moteur.
- Champs – Il s’agit de bobines montées sur des pièces polaires qui génèrent un champ magnétique stationnaire.
- Interpôles – Il s’agit de bobines placées entre les bobines de champ qui génèrent un champ utilisé pour empêcher la formation d’étincelles excessives sur les balais.
- Les flasques – également appelés paliers, sont utilisés pour loger les balais et leurs supports, ainsi que les paliers de l’arbre, qui maintiennent l’armature centrée dans le châssis.
- Montage des balais – Maintient et positionne les balais au-dessus du collecteur de l’induit. En général, un dispositif de tension est utilisé pour maintenir une pression constante sur les brosses.
- Balais – Ils sont utilisés pour fournir du courant continu à l’armature. Les balais se déplacent sur le collecteur.
- Commutateur – Constitué de nombreuses barres de cuivre séparées par du mica. Chaque barre est connectée aux bobines de l’armature.
- Armature – Il s’agit de la partie rotative du moteur qui contient des bobines.
Contrairement à la plupart des moteurs à courant alternatif, les moteurs à courant continu nécessitent une alimentation séparée pour les champs et l’armature. Le courant continu fourni aux champs du stator génère un ensemble de champs Nord et Sud constants. Le courant continu fourni à l’armature génère des champs Nord et Sud qui sont à 90 degrés électriques du champ stationnaire.
Lorsque l’induit génère un couple et se déplace vers le pôle Nord ou Sud approprié, les balais changent de position sur le collecteur, alimentant un autre jeu de bobines à 90 degrés électriques du champ stationnaire. Cela fait de l’induit un composant à courant alternatif car le courant circule dans un sens, en fonction de la position du balai, puis dans un autre sens lorsque le moteur fonctionne.
Les balais sont placés dans une position telle qu’ils sont électriquement “neutres” (pas de courant induit par les champs du stator) afin de réduire les étincelles. Dans la plupart des connexions de moteurs à courant continu, la variation de la tension de l’induit permet de modifier la vitesse de fonctionnement. Un danger général inhérent aux moteurs à courant continu est que si le courant de champ est perdu alors que le courant d’induit est maintenu, le moteur peut décoller et la vitesse augmenter jusqu’à ce que l’induit s’autodétruise.
Les trois types de bobinage de base qui peuvent être utilisés pour identifier le type de moteur à courant continu sont les suivants :
- Série : On les trouve normalement dans les applications qui nécessitent un couple de démarrage élevé. Ils sont constitués d’un ensemble d’enroulements de champ en gros fil et relativement peu de tours, marqués S1 et S2, qui sont connectés en série aux interpôles et à l’induit, marqués A1 et A2 (voir figure 1). Les moteurs connectés en série sont normalement utilisés comme moteurs de traction et ont une très faible résistance de base.
- Shunt: On le trouve normalement dans les applications qui exigent une vitesse constante. Ils se composent d’un ensemble d’enroulements de champ en fil plus petit avec de nombreuses spires, marqués F1 et F2 pour la tension simple et F1, F2, F3, et F4 pour la tension double, et A1 et A2 pour les interpôles et l’induit (voir les figures 2). Les moteurs shunt sont généralement utilisés comme moteurs de grues et de machines-outils et ont une résistance de base relativement élevée.
- Composé: Combine les avantages des moteurs à enroulement série et shunt. Ils fournissent un couple relativement élevé avec une résistance de base à une variation de la vitesse de fonctionnement. Les connexions combinent à la fois les connexions en série et en dérivation (voir la figure 3). Les moteurs composés sont les plus courants et on les trouve couramment dans la fabrication industrielle.
Comme on peut le voir, il y a peu de bobines à comparer les unes aux autres dans une machine à courant continu assemblée. Toutefois, il est possible de mettre au point des procédures pour les essais de bobinage qui permettent d’obtenir un niveau élevé de confiance dans les résultats des essais.
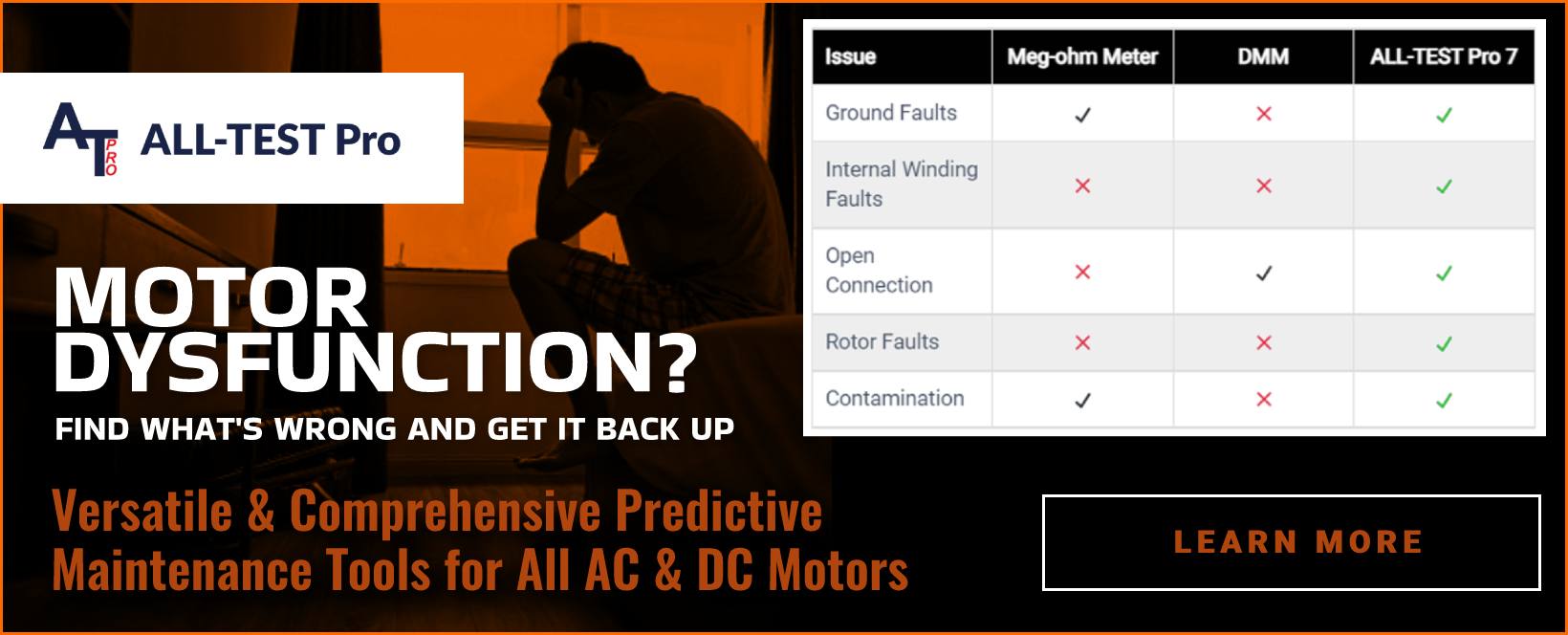
Défauts électriques courants des moteurs à courant continu
Il existe un certain nombre de défaillances électriques courantes des moteurs à courant continu, dont les plus courantes sont décrites ici. Ils résultent de problèmes spécifiques à la conception des moteurs à courant continu en raison de la température, du frottement et des contaminants internes tels que le carbone ou le graphite.
L’une des causes les plus courantes des défauts d’enroulement dans un moteur à courant continu est la contamination de l’enroulement par du carbone ou de la poussière de graphite (carbone) provenant des balais. La poudre fine pénètre dans tous les enroulements fixes et rotatifs et crée un chemin entre les conducteurs ou entre les conducteurs et la terre. Le carbone est souvent piégé et les problèmes sont aggravés par les pratiques de nettoyage et d’entretien lorsque le carbone est soufflé avec de l’air comprimé ou que l’armature est nettoyée et cuite. Dans l’un ou l’autre cas, le carbone peut se trouver serré dans les coins, généralement juste derrière le collecteur. Cela se traduira par un défaut de masse ou un court-circuit au niveau de la connexion du collecteur.
Un autre défaut courant, qui n’est souvent pas pris en compte, est le refroidissement de la machine à courant continu. Cela peut être dû à l’obstruction des passages de refroidissement, à une rotation trop lente de l’armature sans refroidissement supplémentaire, ou à l’encrassement des filtres (le défaut le plus courant lié au refroidissement). La température est le plus grand ennemi des équipements électriques, en particulier du système d’isolation, dont la durée de vie sera réduite de moitié pour chaque augmentation de 10 degrés centigrades de la température (règle empirique acceptée). Au fur et à mesure que l’isolation s’affaiblit, sa fiabilité diminue jusqu’à ce que des défauts d’enroulement entre spires se produisent. Outre la dégradation du système d’isolation, les balais se dégradent également plus rapidement, ce qui entraîne une usure accrue du collecteur et une contamination supplémentaire des enroulements par le carbone.
Un autre défaut lié à la chaleur est généré par des pratiques où les champs sont excités alors que l’armature est au repos (désexcitée). Il s’agit d’un mode de fonctionnement courant qui nécessite un ventilateur distinct pour refroidir le moteur, lequel est normalement équipé de filtres qui doivent être maintenus propres. Ce type de défaut entraîne normalement un court-circuit des bobines de shunt, ce qui réduit la capacité du moteur à produire un couple, et peut aboutir à une condition dangereuse de survitesse de l’induit s’il n’est pas entretenu correctement.
Le collecteur offre également la possibilité de détecter des défauts, ainsi qu’un indicateur du fonctionnement et de l’état du moteur. Un moteur à courant continu fonctionnant correctement aura une fine couche de carbone sur le collecteur et les barres seront uniformes. Des barres de collecteur brûlées, un vitrage strié, une forte teneur en carbone ou une surchauffe du collecteur indiquent des problèmes potentiels qui doivent être résolus.
Test d’armature
Les armatures à courant continu sont les composants les plus longs mais les plus faciles à tester. Trois méthodes de base seront présentées : la méthode des tendances, la méthode des assemblages et la méthode des désassemblages. Dans le cas des tendances, toutes les mesures sont utilisées, cependant, dans le cas des essais montés et démontés, une mesure d’impédance de barre à barre sera utilisée. L’impédance est considérée parce que l’armature est un composant alternatif et que de simples mesures de résistance peuvent manquer certains défauts, notamment les courts-circuits et les mises à la terre. Les tendances seront examinées dans une procédure globale de tendances pour les moteurs à courant continu plus loin dans cet article.
Pour tester l’armature d’un moteur à courant continu assemblé, la meilleure méthode consiste à effectuer ce que l’on appelle communément un test barre à barre en utilisant les balais du moteur. Dans le cas d’un moteur à courant continu qui a deux balais, aucun des balais ne doit être relevé, dans le cas d’un moteur à courant continu qui a quatre jeux de balais ou plus, tous les jeux sauf deux à 90 degrés les uns des autres doivent être relevés, ce qui les fait sortir du circuit de test. Veillez à maintenir un bon contact sur le collecteur en vous assurant que plus de 90 % de la brosse est en contact avec les barres du collecteur et que ces dernières sont propres. S’ils ne sont pas propres, polissez doucement l’armature, en utilisant une méthode approuvée, avant de procéder au test. Si le collecteur est très usé, il devra être démonté et le collecteur devra être “tourné et détalonné”, auquel cas un essai barre à barre démonté serait approprié. Une fois réglé, marquez la position d’une barre sur le collecteur, puis amenez la barre dans une position où elle se trouve juste sous le bord d’attaque de l’un des balais. Dans le test assemblé, vous couvrirez probablement au moins une barre et demie avec le pinceau. Effectuez un test d’impédance, notez la lecture et déplacez l’induit de sorte que le bord d’attaque du balai se trouve au-dessus de la barre de collecteur suivante. Prenez la lecture d’impédance suivante et continuez jusqu’à ce que chaque barre ait été testée. Un bon résultat montrera un modèle cohérent, tandis qu’un modèle incohérent identifiera une armature de mauvaise qualité.
L’essai barre à barre démonté est similaire à l’essai monté, à l’exception du fait que l’armature est hors du cadre et que le testeur a un accès complet au collecteur. Dans ce cas, le testeur utilisera un dispositif de fixation de l’armature ou des fils de test pour se connecter d’une barre à l’autre. L’espacement entre chaque lecture d’impédance doit être constant et à environ 90 à 180 degrés l’un de l’autre. La première barre doit être marquée et l’essai se poursuit jusqu’à ce qu’une jambe du dispositif d’essai ou du fil d’essai ait fait 360 degrés autour du collecteur. Marquez l’impédance pour chaque test de barre à barre puis vérifiez qu’il y a un modèle cohérent.
Test des moteurs de la série
Les moteurs électriques en série sont très difficiles à dépanner car ils ne fournissent pas d’ensembles de champs auxquels se comparer. Les relevés peuvent être effectués de S1 à S2 et de A1 à A2, puis faire l’objet d’une tendance dans le temps ou être comparés à d’autres machines similaires.
Lorsque l’on suit l’évolution des relevés dans le temps, les relevés de résistance simples doivent être corrigés en fonction de la température, généralement par rapport à 25oC. L’impédance et l’inductance ont normalement un changement limité dû à la température tandis que l’angle de phase et les lectures I/F resteront constants, indépendamment de la température. Les variations de l’I/F et de l’angle de phase indiquent des tours court-circuités, tandis que les variations de l’impédance et de l’inductance indiquent normalement des enroulements sales.
La comparaison de moteurs similaires nécessitera des informations supplémentaires. L’opérateur devra s’assurer que le moteur est du même fabricant et du même modèle, ainsi que de la vitesse, de la puissance, etc. Le moteur “modèle” doit être neuf ou reconstruit selon les spécifications du fabricant d’origine. Lors des relevés comparatifs, la température d’essai doit être similaire d’un moteur à l’autre, mais les relevés de l’I/F et de l’angle de phase peuvent être directement comparés. Ces relevés ne doivent pas changer de plus de +/- 2 points pour I/F et +/-1 degré pour l’angle de phase. Une erreur fréquente lors de la reconstruction des bobines d’excitation en série, bien que moins fréquente que pour les bobines shunt, est le remplacement incorrect de la taille des fils, ce qui aura un impact sur la capacité du moteur à générer du couple.
Test des moteurs shunt
Les moteurs shunt à double tension permettent de comparer deux jeux d’enroulements, tandis que les moteurs à simple tension auront la même procédure d’essai que les enroulements des moteurs en série, en utilisant F1 et F2 plutôt que S1 et S2.
Avec la double tension, les enroulements de shunt sont étiquetés F1 à F2 et F3 à F4, ce qui permet à l’analyste de tester et de comparer ces deux ensembles d’enroulements.
Lors du test et du dépannage des lectures dans le temps, les lectures de résistance simple doivent être corrigées en fonction de la température, généralement par rapport à 25oC. L’impédance et l’inductance changeront davantage qu’un moteur à enroulement en série en raison de la résistance simple plus élevée du circuit. L’angle de phase et l’I/F resteront constants, à 1 ou 2 points près, quelle que soit la température. Les variations de l’I/F et de l’angle de phase indiquent des tours court-circuités, tandis que les variations de l’impédance et de l’inductance indiquent normalement des enroulements sales. Les comparaisons entre F1 et F2 et F3 et F4 doivent être inférieures à 3 % en ce qui concerne la résistance, l’inductance et l’impédance et ne doivent pas différer de plus d’un point en ce qui concerne l’I/F ou l’angle de phase.
Les moteurs similaires peuvent être testés et comparés de la même manière que les moteurs à enroulement en série. Dans la mesure du possible, les moteurs doivent être testés, lors de l’établissement de la tendance des relevés, à la même température que les tests précédents. Par exemple, dans les minutes qui suivent l’arrêt des équipements en fonctionnement ou avant le démarrage des équipements, cela permet d’effectuer les tests à des températures similaires.
Essai de moteur à courant continu composé
Les tests sur place, les tendances et le dépannage sont beaucoup plus simples avec un moteur compound. Les moteurs composés à simple tension sont normalement étiquetés A1 à A2, S1 à S2, et F1 à F2, et les moteurs composés à double tension sont normalement étiquetés A1 à A2, S1 à S2, F1 à F2, et F3 à F4. Un point supplémentaire clé d’un moteur à enroulement composé est que l’enroulement série est normalement enroulé au-dessus de l’enroulement shunt, ce qui permet d’éventuels défauts entre ces deux enroulements.
Dans le cas d’un moteur compound, les essais sont normalement effectués sur les bornes du variateur CC. Les tests MCA standard utilisant l’ALL-TEST impliquent des signaux à basse tension et à haute fréquence qui n’endommageront pas l’électronique de sortie de l’équipement, réduisant ainsi la nécessité de déconnecter les fils du variateur pendant le test. Toutefois, si l’analyste souhaite vérifier la résistance d’isolement entre les enroulements série et shunt, les fils doivent être déconnectés du variateur. Lors de l’analyse des tendances à partir du variateur CC, testez A1 à S2 et les deux fils de champ, puis effectuez un test de résistance d’isolement de 500 volts entre les fils S2 et F1 et comparez avec les tests précédents ou des moteurs similaires. Dans les deux cas, les lectures de résistance d’isolement doivent rester supérieures à 100 Meg-Ohms.
L’unité ALL-TEST permet à l’analyste de comparer immédiatement les lectures passées et présentes comme une vérification rapide permettant à l’analyste de prendre une décision rapide pour tester les enroulements plus en profondeur. Comme mentionné dans les techniques de test des moteurs en série et en dérivation, les lectures de l’I/F et de l’angle de phase ne devraient pas changer de plus d’un point entre les tests. Cependant, avec le temps, les enroulements en série et les enroulements de champ varieront considérablement les uns des autres.
Le dépannage des moteurs composés doit être effectué au niveau du moteur lui-même. Débranchez tous les fils du moteur et séparez-les. Testez les enroulements série et de champ comme indiqué dans les instructions relatives aux enroulements série et shunt, puis effectuez un test de résistance d’isolement entre les enroulements série et shunt, la résistance d’isolement doit être supérieure à 100 Meg-Ohms.
Notes sur les essais de moteurs à courant continu du MCA
Les essais MCA sur tout type de moteur à courant continu permettent de dégager plusieurs points essentiels :
- Toute lecture I/F en dehors de la plage de -15 à -50, par exemple -56, indique un défaut d’enroulement.
- Si le test montre une résistance infinie entre les fils d’un même circuit, cela indique un enroulement ouvert.
- Une augmentation de la résistance simple entre les tests, corrigée en fonction de la température, indique une connexion lâche, en particulier lorsque les lectures d’impédance et d’inductance changent. Une résistance simple réduite, corrigée en fonction de la température, peut indiquer un court-circuit, généralement accompagné de modifications de l’impédance, de l’inductance, de l’angle de phase et de l’I/F.
- Lorsque vous testez des moteurs de ce type, l’I/F et l’angle de phase ne doivent pas changer de plus de 2 points, toute différence supérieure à ce chiffre doit entraîner une analyse complète.
- Les changements survenus lors du test du circuit de l’induit doivent entraîner un test de barre à barre.
En suivant ces instructions simples, l’utilisation d’un dispositif MCA vous permettra de détecter les défauts précoces bien avant que l’équipement ne tombe en panne pendant son fonctionnement. Si les tests sont effectués dans le cadre d’un programme de maintenance prédictive, l’intervalle doit être au moins celui indiqué dans le tableau 1.
Tableau 1 : Fréquence d’essai du moteur à courant continu
Type de test | Non critique | Général | Critique |
Entretien général | 1 an | 6-9 mois | 3-6 mois |
Maintenance prédictive | 6 mois | 3 mois | 1 mois |
Test d’armature | 1 an | 6 mois | 3 mois |
Les tests de maintenance générale sont ceux qui ne font pas l’objet d’une tendance dans le temps. Elle s’accompagne généralement d’un contrôle des vibrations, d’un graissage des roulements, d’une inspection du collecteur et d’une inspection des balais. Les tests de maintenance prédictive impliquent normalement des relevés de tendances dans le temps afin de détecter des défauts potentiels, puis de déterminer le meilleur moment pour déposer le moteur en vue d’une maintenance corrective. Lorsqu’un défaut potentiel est détecté, la fréquence des tests doit augmenter jusqu’à ce qu’il soit déterminé que le moteur doit être retiré. Un test complet de l’induit doit être effectué en même temps qu’un test de maintenance générale ou prédictive en raison des contraintes élevées au niveau du collecteur et de la contamination par le carbone.
Conclusion
Le test électrique général des moteurs électriques à courant continu est rendu beaucoup plus facile grâce aux nouvelles techniques disponibles avec l’analyse statique du circuit du moteur. Pour la première fois, il est possible de détecter des défauts de rotation précoces dans les enroulements en série, en dérivation et dans l’induit avant qu’ils ne mettent l’équipement hors service. Les tests de maintenance prédictive peuvent être effectués à partir du variateur, les tests de dépannage étant réalisés au niveau du moteur. En général, les tests sont relativement rapides, nécessitant moins de cinq minutes par moteur pour les tests de maintenance prédictive, avec un temps supplémentaire requis pour le dépannage. Dans l’ensemble, le test MCA améliore considérablement le test des moteurs à courant continu par rapport aux méthodes traditionnelles de tests de continuité.
A propos de l’auteur
Howard W. Penrose, Ph.D., a plus de 15 ans d’expérience dans l’industrie des moteurs électriques et de leur réparation. J’ai commencé comme compagnon réparateur de moteurs électriques dans la marine américaine, puis j’ai assuré le service sur le terrain et l’évaluation d’équipements rotatifs de tous types, de petite à grande taille, en tant qu’ingénieur en chef d’un grand atelier de réparation de moteurs du Midwest. M. Penrose a été directement impliqué dans le rembobinage, la formation et le dépannage d’équipements à courant alternatif, à courant continu, à rotor bobiné, synchrones, de machines-outils et d’équipements spécialisés. Ses autres études portent sur la fiabilité des moteurs électriques et industriels, les méthodes d’essai, l’efficacité énergétique et l’impact de la maintenance sur la production. M. Penrose a été président de la section de Chicago de l’IEEE, président de la Dielectrics and Electrical Insulation Society de l’IEEE Chicago, membre professionnel de l’Electrical Manufacturing Coil and Winding Association, professionnel certifié MotorMaster du ministère américain de l’énergie, analyste des vibrations, analyste des infrarouges et analyste des circuits de moteurs.